Digital Lunch Digestiv
The "Chefs" answer questions you posted on the chat
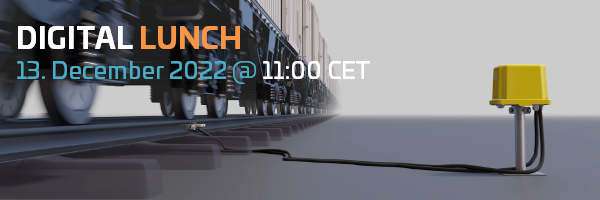
Our current standard lead time is 6 months. Reliable advance order/execution planning might shorten the lead time down to 4 months. Small quantities might be available from stock. However, current world market component crisis has significantly affected current equipment lead time.
By using an asset management system which continuously stores the date offline, the full history is available in case of failure.
This facility is currently not available with the product itself.
A reliable detection of rail breaks is offered by sensors based on rail vehicles. The sensors identify breaks before a track circuit can detect an electrical disconnect in the rail.
Thales wheel sensors do have a clamp type facility for temporary installation, but there is no portable evaluator for temporary use.
The processor boards in the evaluator have physical ethernet connectors on-board. Apart from the cable, no additional equipment is required.
Yes this can be done, but on different side of the track. Closer proximity can be achieved by usage of different sensor operating frequencies.
Thales recommends a drilling machine type "Cembre" or similar. The use of a template will allow for high quality drilling in order to fulfil required tolerances.
Maximum of 48 detection points (a detection point is the combination of a wheel sensor and an electronic unit) can be supervisd by one single evaluator. The magic number is 32 each - sections and detection points can be allocated physically directly to a single axle counter evaluator. A further 16 detection points can be connected via ethernet. Evaluators are able to commicate with each other so that the overall number of detection points and sections is indefinitely scalable.
Wheel sensors for common sections on both gauges can be positioned on the common rail. If the operational conditions require a logical/physical separation of the two gauges then one wheel sensor is required on each separate gauge rail.
Yes. In a redundant system architecture, the failure of a wheel sensor (or detection point) will not have any operational impact.
Yes this can be done. Closer proximity can be achieved by usage of different sensor operating frequencies.
The integration of the counting mechanism into the wheel sensor is currently not foreseen. There are two options for electronic unit (EAK) housing: the standard type EAK30H and the slimline housing type EAK30K.
The evaluator comes with a graphical diagnostic interface, which gives the opportunity to monitor all aspects of operation. It can be connected via a communication network or physically. Integrating the evaluator into an asset management system is posssible due to the interface description which is transparently available in the product documentation. A Thales asset management solution is available for this and can be discussed separately.
The EULYNX protocol (evaluator-interlocking/control system interface) will contain additional information from electronic units, such as passing speed and direction. This feature will be available in the Thales axle counter system Az LM from Release V7.9 on.
Optical cable are cheaper in acquisition and installation and less theft prone. Recent communication networks are usually using fibre optical cable, also due to the bandwidth capabilities which are given. Power to the electronic unit is nevertheless needed but the copper feed from a central point is causing the cost for copper. A local power supply source, with much shorter cable ways from the power source to the power consumer, is giving the chance of reducing this invest and the usage of an existing communication network reduces the CAPEX as well.
While using ethernet, the media it is using does not affect the communication. A copper based communication network is as usable as a well as a fibre based communication network.
Maximum of 48 detection points (a detection point is the combination of a wheel sensor and an electronic unit) can be supervisd by one single evaluator. The magic number is 32 each - sections and detection points can be allocated physically directly to a single axle counter evaluator. A further 16 detection points can be connected via ethernet. Evaluators are able to commicate with each other so that the overall number of detection points and sections is indefinitely scalable.
Wheel sensors for common sections on both gauges can be positioned on the common rail. If the operational conditions require a logical/physical separation of the two gauges then one wheel sensor is required on each separate gauge rail.
A recording of the event is made available. For more information please visit the Thales product web pages at myproducts-thales.com/products.